پلاسٹک چڑھانا ایک چڑھانا عمل ہے جو الیکٹرانکس کی صنعت، دفاعی تحقیق، گھریلو آلات اور روزمرہ کی ضروریات میں بڑے پیمانے پر استعمال ہوتا رہا ہے۔پلاسٹک چڑھانے کے عمل کے استعمال سے دھاتی مواد کی ایک بڑی مقدار کی بچت ہوئی ہے، اس کی پروسیسنگ کا عمل آسان ہے اور دھاتی مواد کے مقابلے اس کا اپنا وزن ہلکا ہے، اس لیے پلاسٹک چڑھانے کے عمل کے استعمال سے تیار کردہ سامان کا وزن بھی کم ہوتا ہے، جس سے اس کا وزن بھی کم ہوتا ہے۔ اعلی میکانی طاقت کے ساتھ پلاسٹک کے حصوں کی ظاہری شکل، زیادہ خوبصورت اور پائیدار.
پلاسٹک چڑھانا کا معیار بہت اہم ہے۔پلاسٹک چڑھانا کے معیار کو متاثر کرنے والے بہت سے عوامل ہیں، جن میں چڑھانا عمل، آپریشن اور پلاسٹک کا عمل شامل ہیں، جو پلاسٹک چڑھانے کے معیار پر نمایاں اثر ڈال سکتے ہیں۔
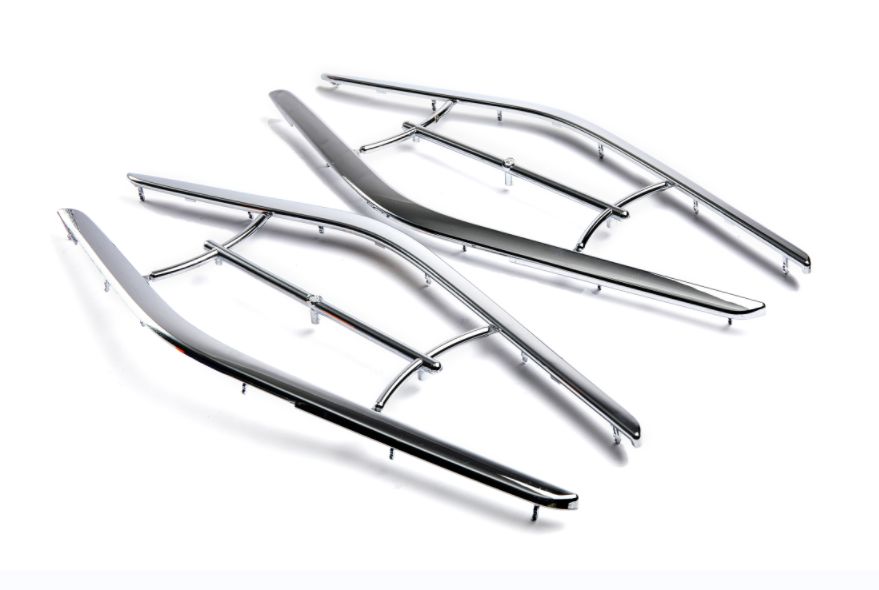
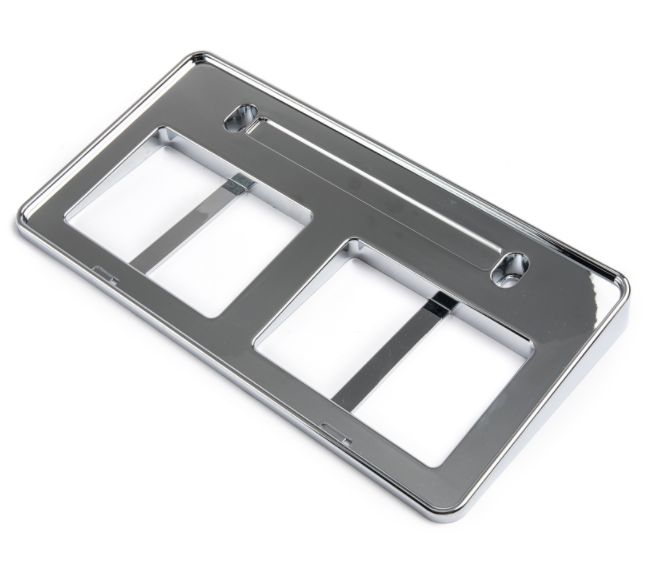
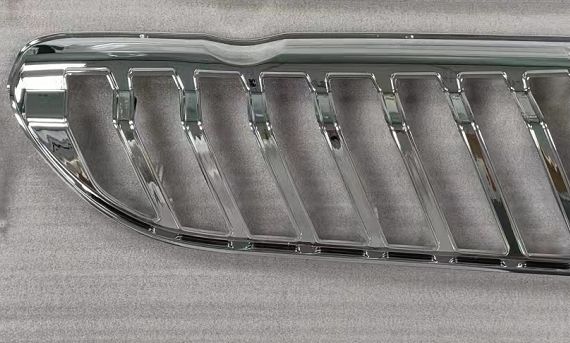
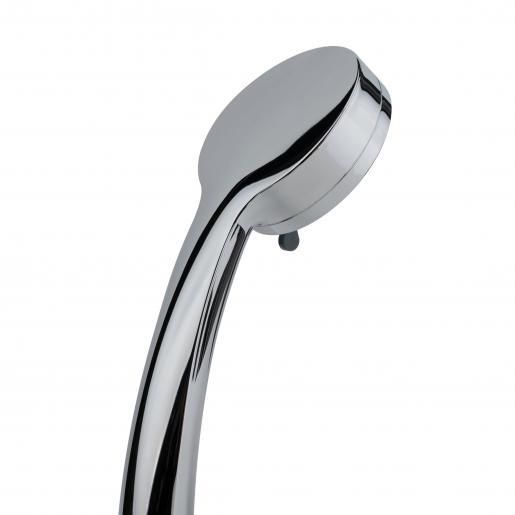
1. خام مال کا انتخاب
مارکیٹ میں پلاسٹک کی بہت سی مختلف اقسام ہیں، لیکن سبھی کو چڑھایا نہیں جا سکتا، کیونکہ ہر پلاسٹک کی اپنی خصوصیات ہوتی ہیں، اور چڑھاتے وقت اسے پلاسٹک اور دھات کی تہہ کے درمیان بانڈ اور جسمانی خصوصیات کے درمیان مماثلت پر غور کرنے کی ضرورت ہوتی ہے۔ پلاسٹک اور دھات کی کوٹنگ۔پلاٹنگ کے لیے فی الحال دستیاب پلاسٹک ABS اور PP ہیں۔
حصوں کی شکل
اے)۔پلاسٹک کے حصے کی موٹائی یکساں ہونی چاہیے تاکہ پلاسٹک کے حصے کو سکڑنے سے بچایا جا سکے، جب پلیٹنگ مکمل ہو جاتی ہے، تو اس کی دھاتی چمک ایک ہی وقت میں زیادہ واضح طور پر سکڑنے کا سبب بنتی ہے۔
اور پلاسٹک کے حصے کی دیوار زیادہ پتلی نہیں ہونی چاہیے، ورنہ پلیٹنگ کے دوران یہ آسانی سے بگڑ جائے گا اور پلیٹنگ کی بانڈنگ خراب ہو جائے گی، جبکہ سختی کم ہو جائے گی اور استعمال کے دوران پلیٹنگ آسانی سے گر جائے گی۔
ب)۔بلائنڈ ہولز سے پرہیز کریں، بصورت دیگر بلائنڈ سولینائیڈ میں موجود بقایا ٹریٹمنٹ سلوشن آسانی سے صاف نہیں ہو گا اور اگلے عمل میں آلودگی کا باعث بنے گا، اس طرح پلیٹنگ کا معیار متاثر ہوگا۔
سی)۔اگر پلیٹنگ تیز دھار ہے، تو چڑھانا زیادہ مشکل ہو جائے گا، کیونکہ تیز دھارے نہ صرف بجلی پیدا کرنے کا باعث بنیں گے، بلکہ پلیٹنگ کو کونوں پر ابھارنے کا سبب بھی بنیں گے، لہذا آپ کو رداس کے ساتھ گول کونے کی منتقلی کا انتخاب کرنے کی کوشش کرنی چاہیے۔ کم از کم 0.3 ملی میٹر۔
فلیٹ پلاسٹک کے پرزوں کو چڑھاتے وقت ہوائی جہاز کو قدرے گول شکل میں تبدیل کرنے کی کوشش کریں یا چڑھانے کے لیے میٹ سطح بنائیں، کیونکہ فلیٹ کی شکل میں ایک ناہموار پلیٹنگ ہوگی جس میں ایک پتلی مرکز اور پلاٹنگ کرتے وقت موٹا کنارہ ہوگا۔اس کے علاوہ، پلیٹنگ گلوس کی یکسانیت کو بڑھانے کے لیے، پلاسٹک کے پرزوں کو ایک بڑے پلیٹنگ سطح کے علاقے کے ساتھ ڈیزائن کرنے کی کوشش کریں تاکہ قدرے پارابولک شکل ہو۔
ڈی)۔پلاسٹک کے پرزوں پر ریسسز اور پروٹریشن کو کم سے کم کریں، کیونکہ گہرے ریسیسز پلاسٹک کو ظاہر کرتے ہیں جب پلیٹنگ اور پروٹریشنز جھلس جاتے ہیں۔نالی کی گہرائی نالی کی چوڑائی کے 1/3 سے زیادہ نہیں ہونی چاہیے، اور نیچے گول ہونا چاہیے۔جب گرل ہو تو، سوراخ کی چوڑائی بیم کی چوڑائی کے برابر اور موٹائی کے 1/2 سے کم ہونی چاہیے۔
ای)۔چڑھائے ہوئے حصے پر کافی ماؤنٹنگ پوزیشنز ڈیزائن کی جانی چاہئیں اور ہینگنگ ٹول کے ساتھ رابطے کی سطح دھاتی حصے سے 2 سے 3 گنا بڑی ہونی چاہیے۔
ایف)۔پلاسٹک کے پرزوں کو مولڈ میں چڑھانے اور چڑھانے کے بعد ڈیمولڈ کرنے کی ضرورت ہوتی ہے، اس لیے ڈیزائن کو اس بات کو یقینی بنانا چاہیے کہ پلاسٹک کے پرزوں کو ڈیمولڈ کرنا آسان ہو تاکہ چڑھائے ہوئے پرزوں کی سطح میں ہیرا پھیری نہ ہو یا ڈیمولڈنگ کے دوران اسے زبردستی کر کے پلاٹنگ کے بانڈنگ کو متاثر نہ کریں۔ .
جی)۔جب knurling کی ضرورت ہوتی ہے، knurling کی سمت ڈیمولڈنگ سمت جیسی اور سیدھی لائن میں ہونی چاہئے۔دھاریوں اور دھاریوں کے درمیان فاصلہ زیادہ سے زیادہ ہونا چاہیے۔
ایچ)۔پلاسٹک کے پرزوں کے لیے جِن کو جڑوں کی ضرورت ہوتی ہے، دھات کی جڑوں کے استعمال سے حتی الامکان گریز کریں کیونکہ چڑھانے سے پہلے علاج کی سنکنرنی نوعیت کی وجہ سے۔
میں).اگر پلاسٹک کے حصے کی سطح بہت ہموار ہے، تو یہ پلیٹنگ پرت کی تشکیل کے لیے سازگار نہیں ہے، اس لیے پلاسٹک کے ثانوی حصے کی سطح پر ایک خاص کھردری ہونا چاہیے۔
3. Mould ڈیزائن اور مینوفیکچرنگ
اے)۔مولڈ میٹریل بیریلیم کانسی کے کھوٹ سے نہیں بلکہ اعلیٰ معیار کے ویکیوم کاسٹ اسٹیل کا ہونا چاہیے۔گہا کی سطح کو 0.21μm سے کم ناہمواری کے ساتھ سانچے کی سمت کے ساتھ آئینے کی چمک کے لیے پالش کیا جانا چاہیے، اور سطح کو ترجیحی طور پر سخت کروم کے ساتھ چڑھایا جانا چاہیے۔
ب)۔پلاسٹک کے حصے کی سطح مولڈ گہا کی سطح کی عکاسی کرتی ہے، لہذا الیکٹروپلیٹڈ پلاسٹک کے حصے کی مولڈ گہا بہت صاف ہونی چاہیے، اور مولڈ گہا کی سطح کی کھردری سطح کی سطح کی کھردری سے 12 درجے زیادہ ہونی چاہیے۔ حصہ
سی)۔تقسیم کی سطح، فیوژن لائن اور بنیادی جڑنا لائن کو چڑھائی ہوئی سطح پر ڈیزائن نہیں کیا جانا چاہئے۔
ڈی)۔گیٹ کو حصے کے سب سے موٹے حصے پر ڈیزائن کیا جانا چاہئے۔گہا کو بھرتے وقت پگھلنے کو جلدی سے ٹھنڈا ہونے سے روکنے کے لیے، گیٹ کو زیادہ سے زیادہ بڑا ہونا چاہیے (عام انجیکشن مولڈ سے تقریباً 10% بڑا)، ترجیحا گیٹ اور اسپرو کے گول کراس سیکشن کے ساتھ، اور اس کی لمبائی اسپریو چھوٹا ہونا چاہئے.
ای)۔ایگزاسٹ ہولز فراہم کیے جانے چاہئیں تاکہ حصے کی سطح پر ایئر فلیمینٹس اور بلبلوں جیسے نقائص سے بچا جا سکے۔
ایف)۔ایجیکٹر میکانزم کو اس طرح سے منتخب کیا جانا چاہئے تاکہ سڑنا سے حصے کی آسانی سے رہائی کو یقینی بنایا جاسکے۔
4. پلاسٹک حصوں کے لیے انجکشن مولڈنگ کے عمل کی حالت
انجیکشن مولڈنگ کے عمل کی خصوصیات کی وجہ سے، اندرونی دباؤ ناگزیر ہیں، لیکن عمل کے حالات کا مناسب کنٹرول اندرونی دباؤ کو کم سے کم کر دے گا اور حصوں کے عام استعمال کو یقینی بنائے گا۔
مندرجہ ذیل عوامل عمل کے حالات کے اندرونی دباؤ کو متاثر کرتے ہیں۔
اے)۔خام مال خشک کرنا
انجیکشن مولڈنگ کے عمل میں، اگر پرزوں کو چڑھانے کے لیے استعمال ہونے والا خام مال کافی خشک نہیں ہے، تو پرزوں کی سطح آسانی سے ہوا کے تنت اور بلبلے پیدا کرے گی، جس کا اثر کوٹنگ کی ظاہری شکل اور بانڈنگ فورس پر پڑے گا۔
ب)۔مولڈ درجہ حرارت
مولڈ کے درجہ حرارت کا پلاٹنگ پرت کی بانڈنگ فورس پر براہ راست اثر پڑتا ہے۔جب مولڈ کا درجہ حرارت زیادہ ہو گا تو رال اچھی طرح بہے گی اور اس حصے کا بقایا تناؤ چھوٹا ہو گا، جو پلیٹنگ پرت کی بانڈنگ فورس کو بہتر بنانے کے لیے موزوں ہے۔اگر مولڈ کا درجہ حرارت بہت کم ہے تو، دو انٹرلیئرز بنانا آسان ہے، تاکہ چڑھاتے وقت دھات جمع نہ ہو۔
سی)۔پروسیسنگ درجہ حرارت
اگر پروسیسنگ کا درجہ حرارت بہت زیادہ ہے، تو یہ غیر مساوی سکڑنے کا سبب بنے گا، اس طرح حجم کے درجہ حرارت میں تناؤ بڑھے گا، اور سگ ماہی کا دباؤ بھی بڑھ جائے گا، جس سے ہموار ڈیمولڈنگ کے لیے ٹھنڈک کا وقت درکار ہوتا ہے۔لہذا، پروسیسنگ کا درجہ حرارت نہ تو بہت کم ہونا چاہیے اور نہ ہی بہت زیادہ۔پلاسٹک کو بہنے سے روکنے کے لیے نوزل کا درجہ حرارت بیرل کے زیادہ سے زیادہ درجہ حرارت سے کم ہونا چاہیے۔مولڈ گہا میں ٹھنڈے مواد کو روکنے کے لئے، تاکہ گانٹھوں، پتھروں اور دیگر نقائص کی پیداوار سے بچیں اور ناقص چڑھانا کے امتزاج کا سبب بنیں۔
ڈی)۔انجکشن کی رفتار، وقت اور دباؤ
اگر ان تینوں میں اچھی طرح مہارت حاصل نہیں کی جاتی ہے، تو یہ بقایا تناؤ میں اضافے کا سبب بنے گا، اس لیے انجیکشن کی رفتار سست ہونی چاہیے، انجیکشن کا وقت جتنا ممکن ہو کم ہونا چاہیے، اور انجیکشن کا دباؤ بہت زیادہ نہیں ہونا چاہیے، جو مؤثر طریقے سے بقایا کو کم کرے گا۔ تناؤ
ای)۔ٹھنڈک کا وقت
ٹھنڈک کے وقت کو کنٹرول کیا جانا چاہئے تاکہ سڑنا کے کھلنے سے پہلے مولڈ گہا میں بقایا تناؤ بہت کم سطح پر یا صفر کے قریب ہو جائے۔اگر ٹھنڈک کا وقت بہت کم ہے تو، جبری ڈیمولڈنگ کے نتیجے میں حصے میں بڑے اندرونی دباؤ پڑیں گے۔تاہم، کولنگ کا وقت زیادہ لمبا نہیں ہونا چاہیے، ورنہ نہ صرف پیداواری کارکردگی کم ہوگی، بلکہ ٹھنڈک سکڑنے سے حصے کی اندرونی اور بیرونی تہوں کے درمیان تناؤ پیدا ہوگا۔ان دونوں انتہاؤں سے پلاسٹک کے حصے پر چڑھانا کی بندھن کم ہو جائے گی۔
ایف)۔رہائی کے ایجنٹوں کا اثر و رسوخ
پلاسٹک کے پرزوں کے لیے ریلیز ایجنٹس کا استعمال نہ کرنا بہتر ہے۔تیل پر مبنی ریلیز ایجنٹوں کی اجازت نہیں ہے، کیونکہ وہ پلاسٹک کے حصے کی سطح کی تہہ میں کیمیائی تبدیلیوں کا سبب بن سکتے ہیں اور اس کی کیمیائی خصوصیات کو تبدیل کر سکتے ہیں، جس کے نتیجے میں پلیٹنگ کی خراب بانڈنگ ہوتی ہے۔
ایسی صورتوں میں جہاں ریلیز ایجنٹ کا استعمال کرنا ضروری ہے، سڑنا چھوڑنے کے لیے صرف ٹیلکم پاؤڈر یا صابن والا پانی استعمال کیا جانا چاہیے۔
پلیٹنگ کے عمل میں مختلف اثر انداز ہونے والے عوامل کی وجہ سے، پلاسٹک کے پرزے مختلف درجات کے اندرونی دباؤ کا شکار ہوتے ہیں، جو پلیٹنگ کی بانڈنگ میں کمی کا باعث بنتا ہے اور پلیٹنگ کے بانڈنگ کو بڑھانے کے لیے مؤثر پوسٹ ٹریٹمنٹ کی ضرورت ہوتی ہے۔
اس وقت، گرمی کے علاج اور سطح کو ختم کرنے والے ایجنٹوں کے ساتھ علاج کا استعمال پلاسٹک کے حصوں میں اندرونی دباؤ کے خاتمے پر بہت اچھا اثر رکھتا ہے.
اس کے علاوہ، چڑھایا حصوں کو پیک کرنے اور انتہائی احتیاط کے ساتھ معائنہ کرنے کی ضرورت ہے، اور چڑھایا حصوں کی ظاہری شکل کو نقصان پہنچانے سے بچنے کے لیے خصوصی پیکیجنگ کی جانی چاہیے۔
Xiamen Ruicheng Industrial Design Co., Ltd کے پاس پلاسٹک پلاٹنگ کا بھرپور تجربہ ہے، اگر آپ کو کوئی ضرورت ہو تو بلا جھجھک ہم تک پہنچیں!
پوسٹ ٹائم: فروری-22-2023